It's also worth noting that VD calculations we do assume that the entire 'maxim load' of a circuit is applied at the worst possible point on the circuit (e.g. the most distant point of a radial) - which is a situation which will very very rarely be encountered in a sockets or lighting circuit (although it may occur in things like shower, cooker and immersion circuits)
I remember when the 17th arrived, and we moved from 4% for all, to 3% lighting and 5% for the rest, I tried to work out how the calculation had gone from 88 meters in a ring final to 106 meters. Try as I could, I could not come up with 106 meters, at that time I was a member of the IET, so on one of their meeting I asked.
And it seems Design current for circuit Ib was taken at 26 amps, it was 20 amps at centre, and 12 amps even throughout the ring final. One also had to consider the Correction factor Ct, as the Tabulated current-carrying capacity of a cable It was 42 amps, I found it was so easy to make an error, only way was to build a JavaScript program so I could feed in known valves with results to test the program had no errors.
I still use it today
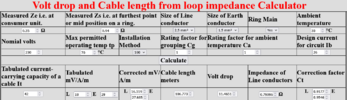
I built it as worried if I made an error, years latter someone could have a claim, however once built, I realised the loop impedance tester is really not accurate enough to show error made unless it was huge, measure the look impedance twice, and you can easily have 0.02Ω difference, it needs measuring twice, so 0.04Ω and the whole differential is only 0.59Ω so although in theory one can work out the volt drop, in practice not that easy.
The idea was I could run JavaScript on my mobile, but knowing 0.59Ω was the difference, one does not really need to work it out, and with a ring final, you need to find the centre. Hence, normal is R1+R2 etc.
I have once installed a supply which had to be re-done with thicker cable, lucky for me, I raised my concerns before we started, so the error was my bosses, it was the supply to a shrink wrap machine, which was rather sensitive to volt drop, there was another where we had problems with volt drop on the supply to a radial of fluorescent lights, but more down to lights drawing over the rated current with a high voltage, lucky was a 110 volt and using auto transformers, so first 20 set to 127 volts and last 5 to 110 volts.
So in the real world unusual to have a problem. But as said all too easy to make a mistake with the maths, so once calculator built, never did it the long way again.