- Joined
- 5 Feb 2018
- Messages
- 22
- Reaction score
- 2
- Country
I'm very lucky to have two garages, side by side but they both have cement asbestos roof panels which are pretty old and cracked. As a result they let in a lot of water, rendering the garages fairly useless for anything other than storing rubbish i.e the wife's soft furnishings (seriously, I recently removed a skip full of cushions!!).
Quick question: is it roofs or rooves? I digress....
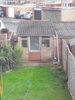
Anyway, I decided to replace the roof with a timber frame and an EPDM one piece rubber cover. I've checked with planning and as long as the roof remains under 2.5m it'll be fine. Building control aren't worried as the garages are detached from the property.
After a few design iterations and a rough attempt at costing the job I cracked on with the work.
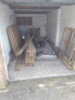
Day one:
First job was to cut a door way between the two garages. FYI: the planning permission was for an extended garage not two separate garages so the permission would still be valid. I screwed some timber battens to the wall to give me a nice straight edge and drilled a load of holes in the mortar joints. I hired a 9" angle grinder for the job. I had read that they kick up LOADS of dust but I really underestimated just how much they generate.
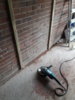
I scoured out the mortar joints every few courses before cutting through the wall so it didn't all fall through in one big old block.
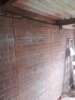
After a few passes with the grinder and a few taps with the persuader the wall fell through nicely.
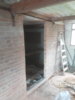
Job done.
Second job was to pour a concrete footing for the timber wall at the end. I was planning on replacing the end wall with a timber frame wall.
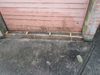
Day two:
I started the second day by cutting the bolts securing the roof panels to the joists. I used some chunky bolt cutters for the job and they pinged off quite happily. I slid the panels down the roof following the fall and being careful not to scrape them too much. Fortunately it was a drizzly day so the panels were wet, reducing the amount of dust generated. In addition I wore an appropriate dust mask, goggles and old clothing that I could get rid of. With a lot of man power and brute strength the panels all came off without breaking them up. Word of warning: this is not a one man job. It dam near killed me.
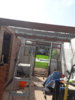
Removing the panels revealed some very rotten joists which were basically held together with cobwebs. In addition, the brick work was very dodgy and big sections were quite wobbly.
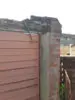
Quick question: is it roofs or rooves? I digress....
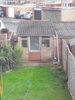
Anyway, I decided to replace the roof with a timber frame and an EPDM one piece rubber cover. I've checked with planning and as long as the roof remains under 2.5m it'll be fine. Building control aren't worried as the garages are detached from the property.
After a few design iterations and a rough attempt at costing the job I cracked on with the work.
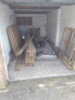
Day one:
First job was to cut a door way between the two garages. FYI: the planning permission was for an extended garage not two separate garages so the permission would still be valid. I screwed some timber battens to the wall to give me a nice straight edge and drilled a load of holes in the mortar joints. I hired a 9" angle grinder for the job. I had read that they kick up LOADS of dust but I really underestimated just how much they generate.
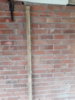
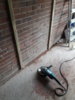
I scoured out the mortar joints every few courses before cutting through the wall so it didn't all fall through in one big old block.
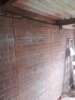
After a few passes with the grinder and a few taps with the persuader the wall fell through nicely.
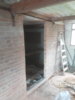
Job done.
Second job was to pour a concrete footing for the timber wall at the end. I was planning on replacing the end wall with a timber frame wall.
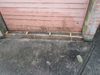
Day two:
I started the second day by cutting the bolts securing the roof panels to the joists. I used some chunky bolt cutters for the job and they pinged off quite happily. I slid the panels down the roof following the fall and being careful not to scrape them too much. Fortunately it was a drizzly day so the panels were wet, reducing the amount of dust generated. In addition I wore an appropriate dust mask, goggles and old clothing that I could get rid of. With a lot of man power and brute strength the panels all came off without breaking them up. Word of warning: this is not a one man job. It dam near killed me.
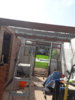
Removing the panels revealed some very rotten joists which were basically held together with cobwebs. In addition, the brick work was very dodgy and big sections were quite wobbly.
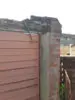