No the plate as it is, is just that slab of plastc, no adjustment.
It doesn't need to be adjustable. It does need to be easy for the lass to knock the flaps up with her feet without trying to bend down to reach it, which would be dangerous.
The foot shapes you can see are there (actually a different chair) just for anti-slip I think.
First thing I looked at was buying slabs of plastic. You can get the stuff, £30-£40 for not much, but I don't know much about working with them. You glue ABS with solvent and ABS sawdust, apparently. Use slow, sharp tools, etc.
Both the mother and the Occ Therapist were anti any ridges or open joins.
Parents can be a problem, they want to lay down th has to be, so they can feel important, though what they say often doesn't make sense or doesn't matter.. This one is bright though and has done her homework.
For a trial I'll slip something over the existing, maybe 4mm ply. That'll tell us about how wide it needs to be, or how wide is too wide. The DMD she has means she can walk a bit, still, but that will get worse. She needs to be able to move her feet freely - but not off the sides which is/will be the natural inclination. But then the ankles grow crooked.
Water would be a problem so I'll have to sand and seal the thing somehow. (It takes hours to do drawings for a 3D printer, but when it's done, it's finished plastic, which saves hours.) Maybe I'll use something like Danish or Tung oil - easier to slap more on than varnish. I guess you don't normally oil plywood!
AS youcan see fromthe pics inthe other thread, the substructure of this thing is steel, so there's scope for straps and f-off magnets. Magnets would be another way to make a step which would "snap" if someone hrave stepped on it
OK next "how would you make this":
This is like a countertop flap hinge: I could maybe just use those but they tend to be too big, and/or the fixings screws would go into the steel tube which I'd rather avoid. Then, again, they aren't designed to be stomped on. Remionder - if the plate is more than 12mm, it won't lift, so I can only increase the edge thickness, where the metal tube isn't. Maybe an inch.
Ctop hinge:
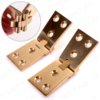
My variations:
Either two pins and a "boat":
or one with just one pin and two under-fingers:
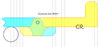
which actually leaves a smooth corner when its folded up
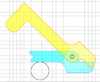
.