I am trying to help my Father in Law fix his sliding garage door. It is a large sectioned wooden door hung on rollers with locating lugs at the bottom of the lower hinges running in a curved metal channel embedded in the garage floor.
The curved element of the bottom channel has rusted away (see pics). I hope to manufacture and fit a new channel replace the curved bit.
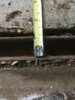
In order to get the curve right, I am planning to drop a plumbline down from the centre of the top rail and draw the resulting arc onto a sheet of OSB. I will then glue and screw 24mm wooden dowels to the OSB on the centreline of the required channel (about 6 inches apart). I am then going to clamp two 2.5m lengths of flat steel (2 or 3mm thick and about 4cm high) either side of the dowels to form the required curved channel. Under the two steels, I will place short lengths of the same material, which I will then weld to the bottom of the curves in order to ‘fix’ the correct shape.
I will then screw the channel in the floor and concrete upto the edges.
Some questions please:
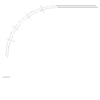
Thanks
The curved element of the bottom channel has rusted away (see pics). I hope to manufacture and fit a new channel replace the curved bit.
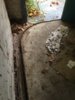
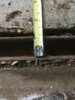
In order to get the curve right, I am planning to drop a plumbline down from the centre of the top rail and draw the resulting arc onto a sheet of OSB. I will then glue and screw 24mm wooden dowels to the OSB on the centreline of the required channel (about 6 inches apart). I am then going to clamp two 2.5m lengths of flat steel (2 or 3mm thick and about 4cm high) either side of the dowels to form the required curved channel. Under the two steels, I will place short lengths of the same material, which I will then weld to the bottom of the curves in order to ‘fix’ the correct shape.
I will then screw the channel in the floor and concrete upto the edges.
Some questions please:
- Does this sound like a sensible approach?
- Will the welded steel tabs actually hold the curve in the correct shape, or will there be any ‘bounce back’?
- Any thoughts on the spacing of the tabs (or the dowels) to actually hold the shape?
- Is 2mm / 3mm steel going to be man enough for the task?
- Is it worth rust proofing?
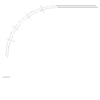
Thanks