Hi,
I have a few tv/satellite points going in, I ordered the faceplates to match our sockets and light switches, the sockets and light switches all fit fine, however I am struggling to fit the tv point.
The clamp for the cable is right at the edge of the pcb with the connection for the signal wire further towards the middle, this means that from what I can tell I need to get the coax to do an immediate bend of at least 90deg - and it's quite thick stuff.. and the clamps aren't that strong so under too much pressure they will pop. I've wondered about trying to put a 'permanent' bend in the coax somehow.. heat, pliers..?
any hints? pic below:
thanks
Trev
I have a few tv/satellite points going in, I ordered the faceplates to match our sockets and light switches, the sockets and light switches all fit fine, however I am struggling to fit the tv point.
The clamp for the cable is right at the edge of the pcb with the connection for the signal wire further towards the middle, this means that from what I can tell I need to get the coax to do an immediate bend of at least 90deg - and it's quite thick stuff.. and the clamps aren't that strong so under too much pressure they will pop. I've wondered about trying to put a 'permanent' bend in the coax somehow.. heat, pliers..?
any hints? pic below:
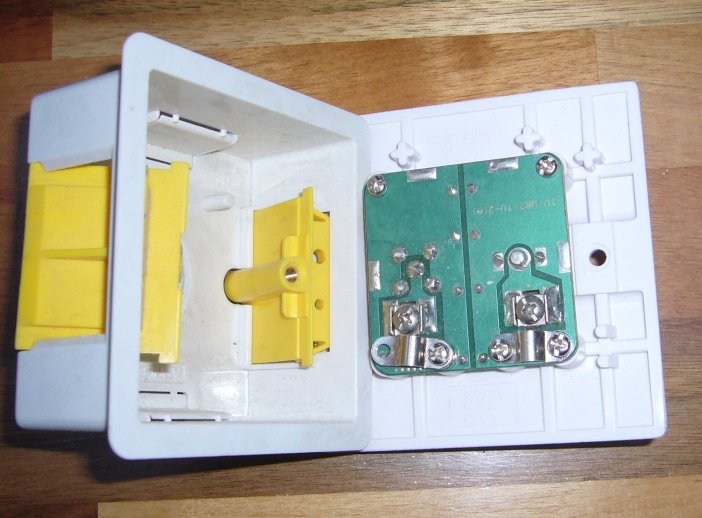
thanks
Trev