Hi. I need to insulate the floor in my utility. It's an unheated single storey outbuilding attached to the back of the main house - an end of terrace with cavity walls. The roof has recently been replaced and insulated (it was corrugated asbestos sheets), and I plan to add external wall insulation for the walls (waiting on planning as I want to have render on top). Because I removed the door between the utility and the main house (the surveyor said it was a hazard as it was one of those nearly all glass ones, untoughened, and near the bottom of the stairs - it's a 50s house), building control say I'm required to insulate the floor which is currently just a concrete slab, which likely doesn't have a damp proof membrane. I will need to do a building notice soon anyway as am adding a shower room to the utility, however I'm unsure on a couple of details on doing the floor. Just wondering if anyone knows if something like the below (the first diagram in the link) would be acceptable to BC - painting on a liquid DPM, frame fixing the timber battens to the floor, PIR between the battens, vapour control layer and then screwing the chipboard to the battens through the vapour control membrane? I want a nice solid floor with minimal/no bounce to it. I'm unclear on whether the frame fixing element and screwing the chipboard down would be ok, as would obviously breach the DPM and vapour control layer. Not sure how I'd get it solid without doing so though! I plan to ask BC as well, but thought I'd see if anyone had done similar?
www.designsindetail.com
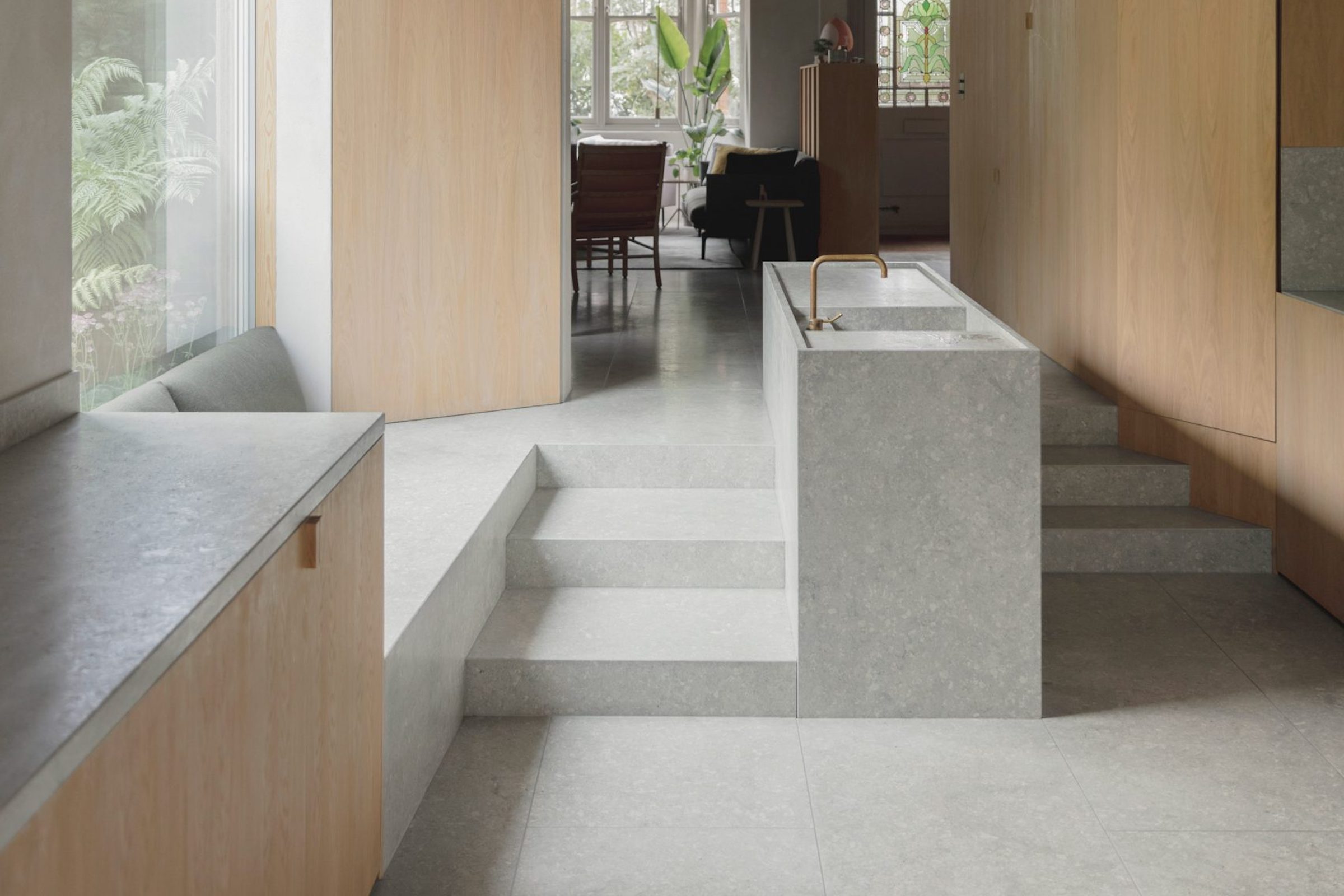
Insulating Concrete Floors: New build and Retrofit Expert Guidance
Insulating Concrete Floors: New build and Retrofit Expert Guidance
