Hi DIYnot forum,
I'm trying to perfect my technique for soldering Yorkshire solder rings and I was hoping some of the experienced experts might be willing to cast a critical eye over my first efforts.
I think I've been preparing these properly: cutting with a pipe slice, reaming the end, cleaning the copper with a gadget (Toolstation 49495) and polishing it with Rothenberger 180 grit strips. LA-CO flux applied (with a brush or latex gloves) evenly to the pipe and lightly inside the fitting. Using a GoSystem swirl flame torch with Map Pro gas.
Q1) 90° elbow: blobs of solder pooling at the bottom of the ring?
I've tried half a dozen of these now and except for the very first attempt I'm getting a disconcerting amount of solder running to the bottom of the vertical ring. Is this pretty typical with these fittings or should it be avoidable every time by improving technique?
I've attached a couple of photos: a couple my efforts look very similar to the first and second photo i.e. thin ring of solder showing except for the blob that was underneath. 3rd is a worse and I don't think I'd be happy fitting something like that. 4th photo is from my first attempt, I think the ring of solder that has flowed out looks quite wide all the way round, but is it acceptable? That 4th one looked like the 2nd photo until I had to reheat a spot that hadn't flowed on the opposite side, which leads me to ask...
Q2) If the solder doesn't fully flow at the first attempt?
On my first test piece I didn't notice a spot on the opposite side hadn't fully flowed, so I took the flame away for more than 30s, but probably less than 2 minutes. It doesn't really matter in this instance since it is just a test piece, but for future reference is taking the flame away for this long and then reheating the solder a terrible idea? I'm just thinking about fixing something in situ where one side is hidden - if it doesn't flow fully on the first heat would you recommend cutting out the offending joint and trying again?
Thanks!
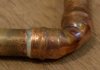
I'm trying to perfect my technique for soldering Yorkshire solder rings and I was hoping some of the experienced experts might be willing to cast a critical eye over my first efforts.
I think I've been preparing these properly: cutting with a pipe slice, reaming the end, cleaning the copper with a gadget (Toolstation 49495) and polishing it with Rothenberger 180 grit strips. LA-CO flux applied (with a brush or latex gloves) evenly to the pipe and lightly inside the fitting. Using a GoSystem swirl flame torch with Map Pro gas.
Q1) 90° elbow: blobs of solder pooling at the bottom of the ring?
I've tried half a dozen of these now and except for the very first attempt I'm getting a disconcerting amount of solder running to the bottom of the vertical ring. Is this pretty typical with these fittings or should it be avoidable every time by improving technique?
I've attached a couple of photos: a couple my efforts look very similar to the first and second photo i.e. thin ring of solder showing except for the blob that was underneath. 3rd is a worse and I don't think I'd be happy fitting something like that. 4th photo is from my first attempt, I think the ring of solder that has flowed out looks quite wide all the way round, but is it acceptable? That 4th one looked like the 2nd photo until I had to reheat a spot that hadn't flowed on the opposite side, which leads me to ask...
Q2) If the solder doesn't fully flow at the first attempt?
On my first test piece I didn't notice a spot on the opposite side hadn't fully flowed, so I took the flame away for more than 30s, but probably less than 2 minutes. It doesn't really matter in this instance since it is just a test piece, but for future reference is taking the flame away for this long and then reheating the solder a terrible idea? I'm just thinking about fixing something in situ where one side is hidden - if it doesn't flow fully on the first heat would you recommend cutting out the offending joint and trying again?
Thanks!
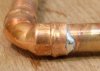
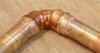
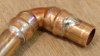
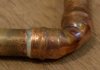